Sent to you by Salamandra (Phillip) via Google Reader:

Ya hemos comentado muchas veces que las ambiciones humanas en términos aeronáuticos casi pueden resumirse en una sola idea: el ahorro de peso. Hemos visto cómo este criterio domina el diseño de todos los aviones actuales y por qué (dinero, obviamente). Y, últimamente, la mejor forma de ahorrar peso que han encontrado los humanos son los materiales compuestos, o composites.

En realidad los materiales compuestos son muy antiguos. La naturaleza tiene los suyos, como el hueso (formado por fibras de colágeno y una matriz de hidroxiapatita) o la madera (fibras de celulosa en una matriz de lignina), pero los propios humanos llevan siglos utilizándolos sin saberlo (no sé por qué no me sorprende). Las antiguas casas de adobe, que ya se hacían en la época del imperio egipcio, son un buen ejemplo de material compuesto, junto con el hormigón, introducido por los romanos.

Pero los humanos sólo comenzaron a darse cuenta de las verdaderas posibilidades de este tipo de material hasta hace bien poco, hacia la segunda mitad del siglo XX. Y es que las propiedades de los composites son verdaderamente asombrosas, si se comparan con las de los elementos que los constituyen. La mayoría de los materiales compuestos están formados por una matriz y un agregado que se refuerzan mutuamente.

En la industria aeroespacial se suelen utilizar FRP's (Fiber Reinforced Plastics): fibras de alta resistencia (fibra de carbono, de vidrio o aramidas) en una matriz de polímero, normalmente una resina termoplástica o termoestable (casi siempre termoestable, y particularmente resina epoxy). Intuitivamente todos sabéis que las fibras funcionan muy bien para aguantar fuerzas de tracción, pero que no sirven para aguantar compresiones. Es decir, cualquier chorlito me diría que una cuerda es perfectamente adecuada para atarle un peso y dejarlo colgar, pero seguro que casi nadie sugeriría utilizarla para sostener algo a modo de columna.

En el caso de las fibras de alta resistencia esto también se cumple, con la diferencia de que la fuerza de tracción que pueden llegar a aguantar es bastante mayor que la que soportaría una cuerda normal y corriente (para que os hagáis una idea: una fibra de carbono de las más resistentes, de un milímetro de diámetro, soportaría unos 450 kilos). Impregnadas con resina posteriormente endurecida (o curada, que es lo mismo, pero queda mejor), no pierden sus buenas propiedades para resistir las tracciones, y además la resina se encarga de soportar las cargas de compresión, con lo que se tiene un material que puede trabajar en cualquier condición de carga. Y, sobre todo, muy ligero, bastante más que cualquier metal.

Sin embargo, no todo son ventajas. Los materiales compuestos deben ser fabricados desde cero y atendiendo a sus peculiaridades, que son muchas. Los procesos de fabricación son la mayoría de las veces complejos y costosos, y en muchos casos deben hacerse a mano, algo que suele fastidiar bastante a los humanos, porque son conscientes de lo propensos que son a meter la pata (al menos lo reconocen).

Alguien que quiera fabricar algo con materiales compuestos tiene varias opciones entre las que escoger. La fibra puede comprarse en forma de tejido (trenzada como si fuera una tela) o cinta (con todas las fibras alineadas en la misma dirección), seca o ya preimpregnada con la resina apropiada (sin curar, claro). En el caso del preimpregnado, lo que suele hacerse es apilar varias capas unas encima de otras, sobre un molde que les dé la forma necesaria. Algunas veces se hace con máquinas, pero es frecuente que el apilado sea manual, y además el número de capas y la orientación que se les dé influyen muchísimo en la resistencia final que tendrá la pieza (y si el operario se deja una arruga, por pequeña que sea, ya está el lío armado). Después habrá que curar la resina para que la pieza tome su consistencia y sus propiedades finales, para lo que suele ser necesario introducirla en un autoclave (un horno que, además de las altas temperaturas, también somete a la pieza a grandes presiones).
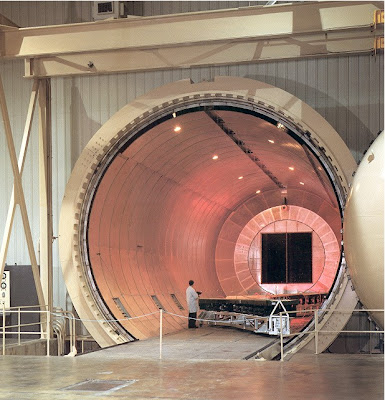
Otro método muy empleado, y cada vez más, es el moldeo por transferencia de resina, o RTM. En este caso se utiliza un tejido seco al que ya se le ha dado la forma de la pieza, metido en un molde hermético en el que se hace el vacío y se inyecta la resina a presión. El objetivo es que la resina se distribuya uniformemente y en el menor tiempo posible por toda la preforma, para después curarla y sacar la pieza hecha. Montar un sistema de fabricación por RTM es complejo, pero una vez hecho el ritmo de producción y los costes son bastante mejores que en el caso del apilado (y, además, se hace todo con máquinas, con lo que los humanos no meten las manazas en el proceso).

Otra de las grandes pegas de los materiales compuestos es que, aunque son bastante resistentes cuando están intactos, esa resistencia disminuye drásticamente si ya hay daños en el material. Un simple golpe producido por la caída accidental de una herramienta desde la mano de nuestro hábil operario podría mellar el material lo suficiente como para que no soportara las cargas en vuelo. Si el golpe es visible, puede repararse y no hay mucho problema, pero muchas veces no queda apenas marca que el ojo (humano) pueda distinguir, lo que se llama BVID (Barely Visible Impact Damage). Por eso las piezas de material compuesto se diseñan con un criterio de tolerancia al daño: la seguridad del avión no debe verse comprometida por la presencia de fallos que no se puedan detectar a simple vista bajo determinadas condiciones. La pieza debe aguantar.

Recientemente han «inventado» un material que podría solucionar este problema en las futuras generaciones de aviones, algo muy importante si se tiene en cuenta que ya tanto el B-787 como el A350 tienen estructuras primarias fabricadas con material compuesto: los composites que se reparan solos. Por supuesto, como siempre, el invento está sacado directamente de la naturaleza, y esta vez ni se molestan en disimularlo. La idea es utilizar fibras huecas como capilares, a semejanza de los vasos sanguíneos de los animales, por los que circulen resina epoxy y endurecedor por separado, de tal manera que el material «sangre» al producirse el daño y ambos agentes se mezclen, endureciéndose y «cicatrizando» la herida. Un tinte mezclado en la resina ayuda a localizar las posibles cicatrices.
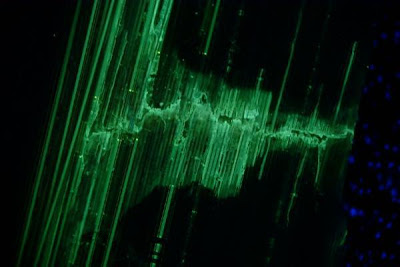
Y, por supuesto, quieren llevarlo más allá, integrando una red completa de vasos sanguíneos, un sistema circulatorio que pudiera ser rellenado o que incluso sirviera para distribuir energía o regular el calor (ya que se ponen a imitar, que lo hagan en condiciones, ¿no?). En unos cuatro años, calculan, estos materiales estarían disponibles para su uso comercial.
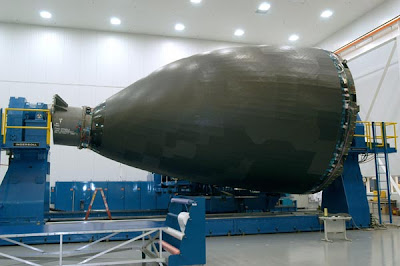
Como curiosidad añadida sobre el tema de los materiales compuestos os dejo un vídeo en el que se hacen pruebas con Pykrete, una mezcla de serrín y hielo que durante la Segunda Guerra Mundial estuvo a punto de utilizarse para fabricar un gigantesco portaaviones. Si será por ideas absurdas…
Imagen del nuevo composite auto-reparable: Engineering and Physical Sciences Research Council. Gracias a jcea y a gizmo por enviar la noticia ;)
Things you can do from here:
- Subscribe to Juan de la Cuerva using Google Reader
- Get started using Google Reader to easily keep up with all your favorite sites
No hay comentarios:
Publicar un comentario